Positive Train Control
Jump to:
Union Pacific is committed to implementing Positive Train Control (PTC) carefully and thoroughly to enhance safety for employees and communities. Through Dec. 31, 2018, we've invested $2.8 billion in PTC, and we plan to spend $115 million in 2019. Our current estimate for PTC's total cost is about $2.9 billion.
About PTC
Positive Train Control (PTC) is an advanced system designed to automatically stop a train before certain accidents occur. In particular, PTC is designed to prevent:
- Train-to-train collisions
- Derailments caused by excessive train speed
- Train movements through misaligned track switches
- Unauthorized train entry into work zones.
PTC does not prevent vehicle-train accidents at railroad crossings, or those due to track and equipment failures.
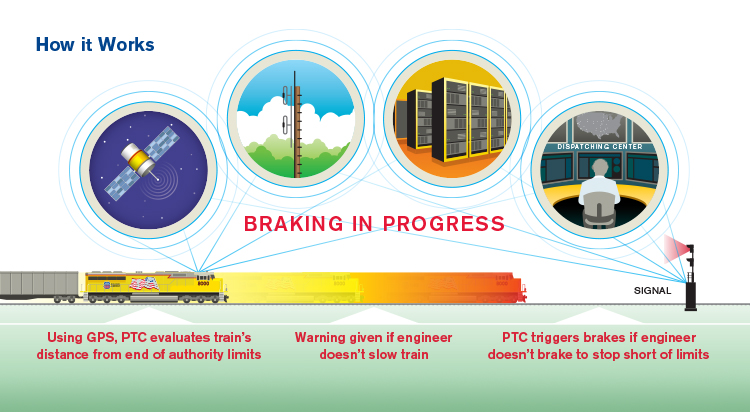
When fully deployed, the nationwide PTC system will accurately determine a train's location, direction and speed via the following process:
- An onboard computer system receives and analyzes track data from wayside locations and base-station radios along the planned route.
- This provides the locomotive engineer with advance warning of movement authority limits, speed limits and track conditions ahead, giving the engineer time to react and bring the train to a safe speed or controlled stop.
- If corrective action is not detected within the warning period, PTC automatically applies the train brakes and brings it to a controlled stop without the engineer's assistance.
Fast Facts: Union Pacific PTC Facts
Union Pacific
- Will invest about $2.9 billion to make PTC operational.
- Equipped 5,515 locomotives and more than 17,000 route miles.
- Installed more than 10,000 wayside antennas and 5,515 locomotive radios.
- Accounts for about a third of the industry's radios, locomotives and route miles required to implement PTC.
Union Pacific is proud of its employees involved in this unprecedented undertaking, as they work tirelessly to safely implement and integrate this new technology.
What PTC Does and Does Not Do
- PTC is an advanced system of technologies designed to automatically stop a train before certain accidents occur. In particular, PTC is designed to prevent:
- Train-to-train collisions
- Derailments caused by excessive train speed
- Train movements through misaligned track switches
- and unauthorized train entry into work zones.
- PTC does not prevent vehicle-train accidents at railroad crossings, stop trains when people are walking on the track, or incidents due to railroad track or equipment malfunctions.
Why PTC is so Complex
Positive Train Control (PTC) is a complex, nationwide system of newly developed technologies that continuously relays critical information such as speed limits, train movement authorization, switch positions, work zone locations and other operational data. It must factor in locomotive and rail car mix; train length, weight and speed; terrain and signal aspects to determine safe stopping distances. This conservatism in the "braking curve" slows the rail network's velocity and, thus, reduces capacity and ability to handle more freight. Additionally, any PTC hardware or software component failure also defaults to stopping the train, thus reducing rail network capacity.
Implementing PTC properly requires integrating thousands of components across the telecommunications spectrum, such as GPS, Wi-Fi, radios, cellular technology, antennae, base stations and first-of-its-kind software that decides when to slow or stop a train – across Union Pacific’s network.
PTC must be "interoperable" – passenger, commuter and freight trains must be able to seamlessly communicate and operate across all railroad systems. Any breakdown in interoperability presents unacceptable risks to the safety and efficiency of America's rail network. Additionally, the Federal Railroad Administration (FRA) must review each railroad's PTC safety plan and certify the PTC system after development and testing of components is completed. This certification is mandatory before PTC-controlled trains can go into service.
About 40 railroads are developing and installing PTC systems around the country. As the architecture of this system comes together, Union Pacific employees and contractors are working full-time against a planned $2.9 billion investment in PTC.
PTC Background and Testing
The Rail Safety Improvement Act of 2008 (RSIA) requires railroads to install PTC systems on tracks that carry passengers or poison- or toxic-by-inhalation (TIH) materials. Based on a January 2012 final Federal Railroad Administration (FRA) rule, the Association of American Railroads (AAR) estimates that PTC technology will be deployed on about 63,000 miles of U.S. freight rail lines. As originally written, the RSIA mandated that PTC be put into service by the end of 2015. Recognizing the challenges of this new technology, in December 2015 Congress extended the PTC implementation deadline to Dec. 31, 2018.