I started my career at Union Pacific Railroad in 1998, switching cars in Iowa. Not long after, there was talk of introducing wireless systems to support rail operations. I was excited. I jumped at the chance to be certified and at the forefront of something that might dramatically revolutionize the industry. Fast forward to today, wireless technology has become widely adopted, making railroad life a whole lot safer and simpler.
Union Pacific continues to harness groundbreaking solutions to redefine operations, enhance safety and expand capacity for future growth – all while keeping the supply chain moving. New technology is advancing productivity across all facets of rail operations, while prioritizing the needs of employees and customers.
Efficient transportation planning requires agile tools that adapt to real-time service interruptions like weather, shifting traffic flows or gateway shutdowns. That’s why we developed the Integrated Transportation Planning (iTP) tool, an AI-driven system built in collaboration with our Tech and Network Planning teams.
iTP helps us optimize network resources, respond swiftly to service disruptions and reduce car handling to accelerate customer delivery times. By minimizing connection points in classification yards, we enhance reliability, shorten transit and open new markets for rail service.
Subscribe to Inside Track
We’ve also transformed how rail cars are grouped and sorted into trains. Historically, classification yards depended on employees using hand signals to coordinate movements. The introduction of radio technology and Remote-Control Operations (RCO) reduced the associated risk of miscommunication, while allowing employees to navigate the yard with greater efficiency and fewer physical demands. It also minimized the time it takes to position cars for their next connecting train.
Three years ago, we introduced DigiCrew, a mobile solution that enables workers to complete tie-up, view or update equipment locations, pull up detailed train lists and much more — all from a handheld device. No longer do workers have to walk to an outdoor kiosk or a building with a computer to do these tasks.
More recently, we advanced further with NX technology, derived from the term “eNtry eXit,” which eliminates manual switch throwing. These innovations enhance safety and reliability and also increase yard capacity since processing cars faster allows us to handle greater volume more efficiently for our customers. NX allows an operator in the terminal to handle cars and can reduce walking distance more than 80% in some locations.
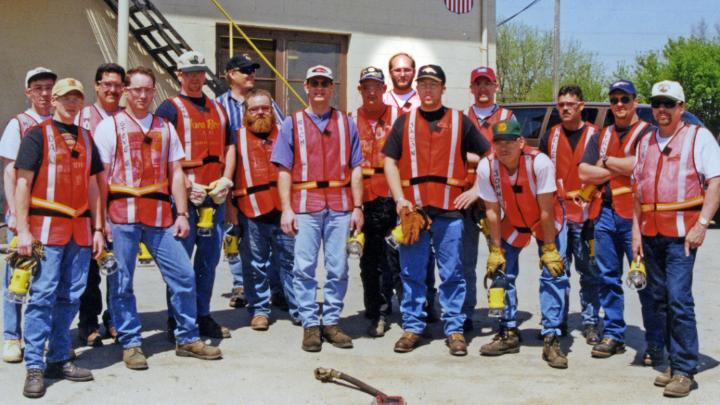
Turner, center, stands with the rest of the May 1998 new-hire Brakeperson class inside the Boone, Iowa, railyard.
Automation is also transforming safety and productivity in Engineering, the group responsible for building and maintaining tracks, bridges and other railroad infrastructure. Our new automated railroad tie unloading equipment, which replaces nearly 2 million ties annually, now unloads 33,000 ties in just 5 to 7 hours instead of 10 days. This technology reduces physical requirements, minimizes mainline disruption and increases capacity without costly infrastructure expansion.
Looking ahead, Union Pacific will continue to reimagine what’s possible by combining technology with human expertise. By collaborating with our frontline employees, we will bring these innovations to life, ensuring technology works in real-world operations while helping our customers grow by improving their supply chains.