Service Update from Beth Whited, CMO
Announcement Number: CN2018-16
Categories: General Announcements
Posted Date: June 8, 2018
To Our Customers,
As we continue to work toward resolving our service challenges, I want to provide another update on our progress.
We continue to be diligent about inventory control, resource allocation and identifying additional adjustments to improve our service network wide. Our strategies for improvement have been effective and our key operational metrics are trending in the right direction, but we still have work to do.
Inventory
We remain committed to reducing inventory levels in order to improve velocity. As a result of these efforts, we’ve seen one of the largest 60-day velocity improvements in the last decade. As network congestion clears, we’ve also seen substantial decreases in freight car dwell, which represents the amount of time cars spend in yards. Since first quarter, dwell is down 11 percent.
Over the last month, operating inventory levels have remained below 200,000 cars on a seven-day basis, our lowest levels since September 2017 even though we have seen a nearly three-percent increase in volume. This means we are moving more freight at faster speeds and are making an impact from a velocity perspective.
Crews
More than 250 graduates from our spring classes are now in the field and actively working to improve service. We are also holding true to our commitment to graduate an average of 200 trainees per month. June through August will be peak graduation season, with more than 700 candidates expected to complete the program and enter the workforce.
Over the course of the next 30-60 days, vacations for train, engine and yard employees will be peaking. As a result, we will continue to manage our crews closely to ensure the best possible crew availability, especially in the Northern Region, where we are recruiting heavily to offset worker scarcity in this less-populated part of the country.
Locomotives
We have pulled approximately 300 locomotives out of storage since early February. A portion of these units are in service to help handle the projected increase in volume over the course of the summer to ensure our ability to serve our customers.
Regional Outlook
The Western Region has improved, as velocity has increased month over month. As we continue to work to reduce inventory at our network yards and the region has fewer track renewal projects in the coming months, we anticipate further improvement. However, the recent tunnel collapse between Eugene and Chemult, Oregon, may delay the anticipated improvement as we work to repair the tunnel and trains in the region are rerouted for a period of days.
Velocity in the Northern Region has improved by three percent since the first quarter. As track renewal crews head into the region, these maintenance-of-way projects may cause some natural headwinds; however, they are important investments in operating a safe and efficient railroad. The core metrics for the region, such as launching trains on time, making car connections in our terminals, and spotting and pulling cars from customer facilities, remain at their best levels since the middle of 2017.
The Southern Region has shown significant performance improvement this month, exceeding last year’s performance. As planned, devoting more crews and locomotives to this area has had a positive effect on service even as the region has successfully managed a track renewal project west of Fort Worth, Texas, and in the yard at Pine Bluff, Arkansas. Similar to the Northern Region, the core metrics are at their best levels since the middle of 2017.
Hurricane Preparedness
In addition to a focus on how to improve service today, we are also looking forward to ensure preparedness of our operations during unplanned events like natural disasters. With the start of hurricane season, we have published a Hurricane Planning & Recovery page that outlines best practices to follow during the hurricane season. This page also includes links to our automated process for customers to report service issues and request diversions online, which improves our ability to provide the proper response during storm events.
Positive Train Control Progress
I’ve mentioned before that the implementation of Positive Train Control (PTC) requires us to work through training, technical and train handling issues that can have an impact on service. For instance, we’ve seen PTC-equipped trains make unintended full stops, which can be caused by both technical issues and human behaviors.
Fortunately, we’ve made significant progress on this matter. On the technical side, system enhancements are reducing the number of unintended full stops. On the training side, a dedicated team in the field is working with crews new to PTC to ensure they are doing their part to prevent unnecessary stops. This team works with our crew members to ensure they understand PTC best practices and to answer any questions they may have.
Likewise, a deep dive into every brake enforcement incident has allowed us to understand the root causes of train stops and help employees in the field take action to prevent them. We have also added resources dedicated to the problem-solving process. Contributing to this effort are newly named Managers of PTC Operations, leaders in the field whose responsibility it is to address the human factors contributing to unintended full stops.
Together, these efforts have reduced train stops by 23 percent since December — and the number of stops continues to trend downward, despite an increase in the number of PTC trains running on our network each month and expanding our PTC footprint. To learn more about how PTC works, take a look at this video.
Thank You
Thank you for your continued patience and cooperation. We will provide additional updates as we work to restore service to normal levels.
We appreciate your business.
Sincerely,
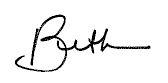
Beth Whited
Executive Vice President & Chief Marketing Officer